Regla de inspección de Hardbanding - ITP Precision
- ITPprecision Instruments & Tools Precision
- 24 mar
- 33 Min. de lectura

Regla de inspección de Hardbanding - ITP Precision
Características Generales:
Fabricante: ITP Precision
Material: Acero inoxidable calibre 16 (1.5 mm, equivalente a 0.0598")
Normas de referencia: API RP 7G-2 y DS-1 Volumen 3
Dimensiones:
Longitud total: 24 pulgadas
Ancho: 3 pulgadas
Espesor: 0.0598" (1.5 mm)
Funcionalidades:
Medición de la altura de Hardbanding: con 6 perfiles con alturas 1/32", 1/16", 3/32", 1/8", 5/32" y 3/16"
Regla graduada de 5" con escalas de 0.125" para una evaluación precisa de la altura del hardbanding.
Evaluación de cambios de sección:
Dos radios:
Radio de 1.5 pulgadas.
Radio de 2 pulgadas.
Tapers:
Taper de 18 grados para inspección del taper del drill pipe.
Taper de 30 grados para la evaluación de la entrada de lodo en conexiones Box con Boreback.
Orificios de evaluación de porosidades:
Permiten la inspección rápida de porosidades presentes en las superficies de la tubería.
Uso:
Este instrumento ha sido diseñado para la evaluación en campo y aplicación de soldaduras de HB nuevas de tuberías revestidas con hardbanding. Sus escalas y perfiles permiten una inspección ágil y precisa según las normativas API RP 7G-2 y DS-1 Vol. 3.

PARTES DE la regla
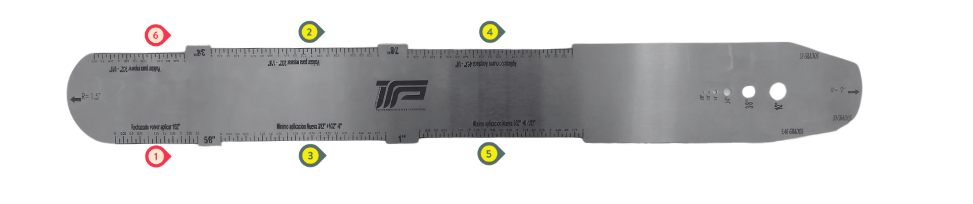
instrucciones de operacion
Inspección Regla ITP Precision:
1) Perfil de 1/32" (0,8 mm) - Esto es para medir la altura de las bandas antiguas. Cualquier cosa de menos de 1/32" (0,8 mm) debe volver a estar endurada. Volver a endurecer las bandas antiguas de más de 1/8" podría dar lugar a bandas inaceptablemente orgullosas. En situaciones extremas, el propietario de la tubería podría optar por volver a endurecer la banda antes de que se alcance el 1/32" (0,8 mm), para no experimentar el desgaste de la junta de la herramienta si las bandas duras se desgastan antes del próximo mantenimiento programado.
2) Perfil de 1/16" (1,6 mm) - Esta es una nueva característica en el medidor y es para la altura mínima de bandas duras en las nuevas aplicaciones de bandas duras de tubos.
3) Perfil de 3/32" (2,4 mm) - El perfil de 3/32" (2,4 mm) es para medir la altura mínima de bandas duras de las nuevas bandas. Las bandas demasiado bajas podrían crear un problema en situaciones extremadamente abrasivas y las bandas duras podrían desgastarse más rápidamente.
4) Perfil de 1/8" (3,2 mm): una vez más, esta muesca más pequeña es una nueva característica del medidor de banda dura e indica la altura máxima de banda dura en las nuevas aplicaciones de tubería.
5) Perfil de 5/32" (4 mm) - Esto es para medir la altura máxima de bandas duras de las nuevas bandas. Para bandas de más de 5/32" (4 mm), se debe consultar al propietario de la tubería. Es importante tener en cuenta que las bandas más orgullosas podrían crear problemas de autorización.
6) Perfil de 3/16" (4,6 mm) - Esto es para medir la altura máxima de bandas duras de las nuevas bandas. Para bandas de más de 3/16" (4 mm), Rechazada.
Cabe señalar que recientemente la altura máxima aceptable de bandas duras ha cambiado de 3/32" +/- 1/32", a 5/32" + 0" y - 1/32".
Recuerde que se prefieren las bandas planas o ligeramente abovedadas, y las bandas cóncavas nunca son aceptables.
Recomendaciones de Mantenimiento y Almacenamiento
Mantenimiento:
Limpieza regular:
Limpie la regla después de cada uso con un paño limpio y seco para eliminar cualquier residuo de aceite, grasa, polvo o suciedad que pueda afectar su precisión.
Si es necesario, use un paño suave humedecido con alcohol isopropílico para remover contaminantes más difíciles.
Protección contra la corrosión:
Aunque la regla está fabricada en acero inoxidable resistente a la corrosión, se recomienda aplicar periódicamente una capa ligera de aceite lubricante (preferiblemente un aceite protector para metales) para evitar la oxidación en ambientes altamente corrosivos.
Inspección visual:
Revise regularmente la regla para detectar cualquier signo de desgaste, golpes o deformaciones que puedan afectar su capacidad de medición. Si la regla está dañada, debe ser reemplazada para asegurar la precisión en las inspecciones.
Calibración periódica:
Aunque la regla está diseñada para mantener su precisión a lo largo del tiempo, se recomienda realizar una calibración anual o después de un uso intensivo para asegurar que las mediciones sigan siendo precisas.
Almacenamiento:
Lugar seco y ventilado:
Almacene la regla en un lugar seco y bien ventilado para evitar la acumulación de humedad, que podría acelerar el proceso de corrosión.
Protección de impactos:
Coloque la regla en un estuche o caja de almacenamiento adecuado para protegerla de golpes o caídas que puedan dañar su estructura o precisión de medición.
Posición horizontal o colgada:
Almacénela en posición horizontal en una superficie plana o colgada en un soporte adecuado para evitar que se deforme. Evite colocar objetos pesados sobre la regla.
Evitar exposición a químicos agresivos:
Manténgala alejada de productos químicos corrosivos o ambientes con vapores ácidos que puedan afectar la integridad del acero inoxidable.

Inspección Dimensional: Las dimensiones de acabado del “hardbanding” deben cumplir con las tolerancias especificadas en la Fig.1. Todas las superficies del “hardbanding” deben cumplir con los siguientes criterios de acabado:
La superficie completa del “hardbanding” debe mecanizarse o esmerilarse de manera concéntrica y perpendicular al eje del “tool joint” hasta producir un acabado superficial menor o igual a 125 m" CLA (Promedio Lineal Calculado) y debe verificarse con un estándar de rugosidad superficial.
Toda la superficie del “hardbanding” debe presentar un diámetro suave (sin cambios abruptos) y constante. No se permiten solapamientos, arrugas, protuberancias u ondulaciones. La única excepción son las pequeñas depresiones entre las bandas individuales soldadas, las cuales son aceptables siempre y cuando no excedan 3,2 mm (1/8 pulg) de ancho o 1,6 mm (1/16 pulg) de profundidad (véase Fig.1).
La cara de intersección entre el “hardbanding” del diámetro externo del “tool joint” y el inicio del bisel debe ser suave y redondeada.
Inspección no Destructiva: La inspección no destructiva del “hardbanding” debe incluir, además de las partículas magnéticas húmedas fluorescentes o tintes penetrantes, la verificación visual y dimensional establecida en esta especificación. En todos los casos se debe inspeccionar el 100% del “hardbanding”, incluyendo 1 Pulg (25 mm) del metal base adyacente a cada lado.
La inspección debe realizarse una vez que los “tool joints” se hayan enfriado por debajo de 50°C (122 °F). A continuación se definen los criterios de aceptación y rechazo que se deben aplicar para evaluar la calidad del “hardbanding”:
Inspección del Acabado: Debido a los altos niveles de esfuerzos residuales en estos recubrimientos duros, suelen presentarse grietas transversales al cordón después de la soldadura, las cuales pueden propagarse a través de los cordones o formando un ángulo entre 30° y 45, interconectándose. Esto es aceptable, siempre y cuando las grietas tengan un ancho inferior a 1,6 mm (1/16 Pulg) y un espaciamiento mínimo entre sí de 12,7 mm (1/2 Pulg). Ver Fig.2.

TIPOS DE DESGASTE
En la industria de perforación, el desgaste entre el casing (revestimiento) y el hardbanding (recubrimiento resistente) del tool joint (unión del tubo) es un tema importante ya que puede afectar la eficiencia y la vida útil de los equipos. Aquí hay una descripción de los modelos de desgaste asociados:
1.Desgaste abrasivo:
1.Causa: Ocurre debido a la fricción constante entre el casing y el hardbanding durante la perforación.
2.Mecanismo: Partículas abrasivas en el lodo de perforación y la formación geológica entran en contacto con la superficie del hardbanding, causando desgaste gradual.
3.Efectos: Reducción de la vida útil del hardbanding y posiblemente daño al casing.
2.Desgaste adhesivo:
1.Causa: La temperatura y la presión durante la perforación pueden provocar la transferencia de material entre el casing y el hardbanding.
2.Mecanismo: Pequeñas partículas de material pueden adherirse a la superficie opuesta, creando una capa adicional que afecta negativamente la fricción y la eficiencia del sistema.
3.Efectos: Pérdida de rugosidad en el hardbanding, disminución del agarre y aumento del riesgo de deslizamiento.
3.Desgaste por fatiga:
1.Causa: Movimientos repetitivos y vibraciones durante la perforación pueden causar fatiga en el material del hardbanding.
2.Mecanismo: La carga cíclica puede conducir a la formación de grietas y fisuras en el hardbanding, especialmente en áreas sometidas a tensiones repetitivas.
3.Efectos: Reducción de la integridad estructural y posiblemente fallo prematuro.
4. Corrosión:
1.Causa: La presencia de fluidos corrosivos en el entorno de perforación puede provocar la corrosión del casing y del hardbanding.
2.Mecanismo: La corrosión puede debilitar la integridad del material y aumentar el riesgo de desprendimiento del hardbanding.
3.Efectos: Pérdida de resistencia y vida útil reducida del tooljoint.
La gestión efectiva de estos modelos de desgaste implica la selección cuidadosa de materiales resistentes, la implementación de prácticas de mantenimiento preventivo y la monitorización regular de las condiciones de los tooljoints durante la perforación.
El desgaste del casing es la remoción no deseada de metal del casing que resulta de la transferencia de energía de la sarta de perforación al casing durante la rotación y el viaje.
• Fuerzas laterales: Para que la carcasa se desgaste, deben estar presentes cargas laterales entre el tool joint y el casing. El grado de desgaste será proporcional a la magnitud de la carga lateral, en igualdad de condiciones.
• Factor de desgaste: El factor de desgaste es otro elemento clave para determinar la tasa de desgaste del casing. El factor de desgaste está muy influenciado tanto por el material del tool joint como por las propiedades del fluido de perforación. La necesidad de reducir el factor de desgaste ha impulsado el uso de bandas duras "amigables" en las juntas de las herramientas.
• Cantidad de movimiento relativo: El grado de desgaste del casing es proporcional a la distancia total que la sarta de perforación se desliza en contacto con el casing.


Nota 1: La dimensión alternativa para H puede ser 3/32" (+0", -1/32") si LE es 3/8" (+1/8", -0").
Nota 2: Si la junta de la herramienta de pasador tiene ranuras de identificación, la dimensión LP puede ser 1-1/2".
Nota 3: La longitud de banda dura en la caja igual a 4" también es una configuración de uso común.
Referencia: La Tabla 5.1 y las Figuras 5.5, 5.6, 5.7, 5.8 y 5.9 presentan datos dimensionales de bandas duras.
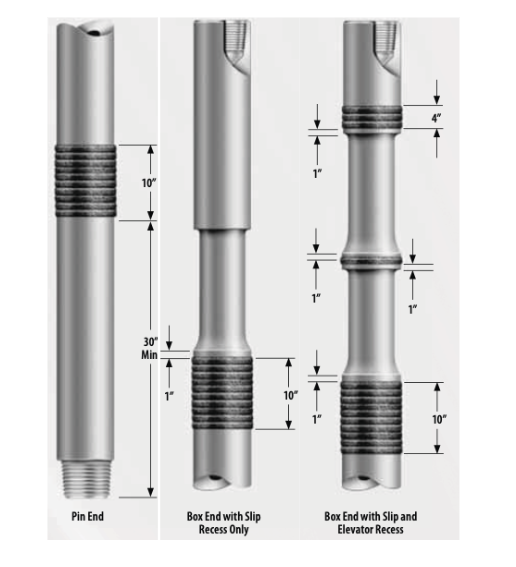
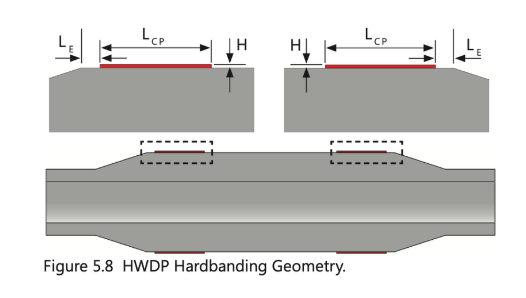
3.22 Re-aplicación de Hardbanding
3.22.1 Propósito
Este procedimiento cubre la inspección de componentes usados a los que se va a aplicar “hardbanding” [incluyendo, pero no limitados a las juntas de herramientas, (tool joints), el recalque central de las tuberías de perforación extrapesadas (HWDP), las botellas (drill collars) y las tuberías de trabajo (workstring tubing)] y los procedimientos requeridos para asegurar la re-aplicación de metal duro con calidad.
3.22.2 Equipo
3.22.2.1 Especificación del Procedimiento de Soldado (WPS)
La especificación del procedimiento de soldado (WPS) para el producto de metal duro específico que se va a aplicar debe ser suministrada por el fabricante de metal duro, y una copia actualizada debe estar disponible en el sitio de trabajo a la hora de aplicar el metal duro. El “WPS” debe proveer, como mínimo, los requerimientos para:
a. Preparación de la Superficie: La rugosidad superficial aceptable, corrosión, agrietamiento (encontrada ya sea visualmente o por ensayos no-destructivos) u otras condiciones que impacten de forma adversa al metal duro.
b. Temperatura y Tiempo de Precalentamiento: La temperatura a la cual el componente se debe calentar, el tiempo que la temperatura se debe mantener antes de aplicar el “hardbanding”, y los métodos de medición para confirmar esta temperatura.
c. Variables de Soldado: Rangos aceptables para lo siguiente Proceso de Soldado (Gas Shielding, Sub Arc, Open Arc, etc).
Velocidad de Rotación.
Velocidad de Alimentación de Alambre.
Requerimientos de Rango de Voltaje.
Rangos de Corriente.
Sentamiento del Soplete (offset, ángulo, arco eléctrico, distancia, etc.)
Ancho del cordón.
Velocidad de oscilación.
Selección del Gas.
Otras variables importantes que requieren monitoreo y control según lo establecido por el fabricante.
d. Rangos de Temperatura de Inter-pase: Rangos de temperatura aceptable para el material del componente, los métodos de medición, y lugar de medición.
e. Tiempos y Temperaturas de Pos-Calentamiento: La temperatura que el material del componente debe mantener después de aplicar el metal duro, la duración de tiempo que la temperatura debe mantenerse, los métodos de enfriamiento (enfriado a aire, aislado, etc.), y los métodos de medición para determinar las temperaturas.
f. Patrones de Agrietamiento Aceptables y Rechazables: Los requerimientos para la inspección visual después de aplicar el metal duro a los componentes y los límites de agrietamiento y otras cuestiones de calidad sobre la soldadura.
g. Registros de la Calificación del Procedimiento (PQR): Un reporte del trabajo metalúrgico hecho para probar que la aplicación de metal duro realizada de acuerdo con este procedimiento (WPS) es aceptable en términos de adhesión y calidad. Un procedimiento recomendado para la prueba de PQR es dado en el DS-1 Volumen 2.
h. Calificación del Desempeño del Soldador (WPQ): Los requerimientos necesarios para que cada soldador pruebe que él o ella sean competentes en el uso de esta especificación (WPS) y es capaz de aplicar “hardbanding” con una calidad aceptable.
i. Enfriamiento de la Superficie Interna: La especificación del procedimiento de soldadura (WPS) debe especificar si es requerido el enfriamiento de la superficie interna para tubería de perforación con plástico interno o si no se debería realizar enfriamiento interno. En caso de requerir enfriamiento interno (ID) por el “WPS”, el procedimiento “WPS” debe proveer los requerimientos para el tipo de enfriamiento, rapidez del flujo, temperatura mínima y máxima del refrigerante y otras variables operacionales que apliquen.
3.22.2.2 Medición de la Temperatura
Un sensor de temperatura de 1000°F como mínimo o un instrumento de medición digital usando un termopar que haya sido calibrado dentro del año pasado. Ver la sección 2.21 para los requisitos de calibración.
3.22.2.3 Otros Aparatos
Se requiere de una regla de metal de 12 pulgadas con graduaciones en incrementos de 1/64-pulgadas, una regla metálica recta y compases externos, también cualquier otro equipo especificado por el procedimiento “WPS”.
3.22.3 Preparación
Precaución: Algunos productos de metal duro no se pueden aplicar encima de otros productos debido a incompatibilidad química o mecánica. La re-aplicación de “hardbanding” nuevo sobre metal duro existente no- compatible puede conducir a problemas como pegamento inadecuado, agrietamiento excesivo, y un pobre desempeño. Se recomienda la examinación de documentación disponible para determinar el tipo o marca de cualquier metal duro ya existente en el componente. Si no se puede determinar el tipo de “hardbanding” existente, se recomienda la remoción del “hardbanding” existente para evitar problemas de incompatibilidad.
a. Toda la tubería se debe numerar en secuencia.
b. Se debe realizar una Inspección Visual de Conexión (Procedimiento 3.11) y Dimensional 1 (Procedimiento 3.12) de todos los componentes antes de la remoción de metal duro o la re-aplicación para asegurar que todos los componentes están en forma para usarse.
c. Se debe contar con copias impresas del procedimiento “WPS” en el sitio. Si surge cualquier conflicto entre esta especificación y los requerimientos del fabricante, aplican los requerimientos del fabricante.
d. Se debe remover totalmente toda grasa ya sea de almacenaje o para roscas de todas las conexiones.
e. Las superficies a soldar deben ser preparadas para “hardbanding” de acuerdo con las instrucciones del procedimiento “WPS”. Esto puede involucrar una inspección visual, inspección no-destructiva, soldadura de metal suave, y/o maquinado para preparar el componente.
3.22.4 Procedimiento
a. Cualquier metal duro existente debe ser examinado visualmente. Si existe descarapelado, despedazado, o huecos mayores de 1/16” en diámetro en cualquier metal duro existente, se debe remover el “hardbanding” presente
b. Si se tiene que remover el metal duro existente, se debe realizar una inspección con partículas magnéticas (Procedimiento 3.9) del área de metal duro más 6 pulgadas a cada lado en la superficie externa del componente después que se ha removido el “hardbanding” existente y que el componente se haya enfriado a la temperatura ambiente. En la Inspección con Partículas Magnéticas deben aplicar los requerimientos de los párrafos 3.9.2, 3.9.3 y 3.9.4 sobre Equipo, Preparación y Procedimiento. Cualquier grieta es causa de rechazo.
c. La superficie a soldar debe ser inspeccionada visualmente. El área en que se va a aplicar metal duro debe tener un acabado metálico brillante y estar libre de materia extraña tal como óxido, grasa, aceite, recubrimiento plástico.
d. Se debe determinar la excentricidad de la superficie a soldar midiendo el diámetro externo (OD) en dos locaciones separadas 900. La excentricidad del área a soldar (diferencia entre las dos mediciones) no debe exceder 0.060 pulgadas. La sección resaltada o levantada de una aplicación de metal duro excéntrica debe esmerilarse concéntrica (dentro de 0.060 de pulgada) antes de cualquier intento de re- aplicación de metal duro o la re-aplicación debería ser aplicada solo al lado raso de la junta y ligada a la aplicación inicial resultando en una aplicación sobresaliente (resaltada) simétrica.
e. El componente debe ser precalentado y la temperatura de precalentamiento monitoreada, según lo requerido por el procedimiento (WPS). El método de precalentamiento debe ser “penetrante” donde el componente se caliente uniformemente en todo su volumen. No se permite calentamiento superficial o local usando soplete u otros medios. Durante el proceso de precalentamiento, no se debe permitir ningún residuo de carbón (tizne) sobre las superficies antes de la aplicación de “hardbanding”.
f. Después que el componente haya alcanzado la temperatura de precalentamiento apropiada (indicada por el sensor de temperatura calibrado) y mantenido a esa temperatura por el tiempo apropiado, se debe aplicar el “hardbanding” al componente según lo especificado en el procedimiento “WPS”. Se debe monitorear los parámetros de soldadura tales como perfil de la banda de soldadura, calidad de la soldadura (porosidad, huecos, sopladuras, etc.), y la altura de la soldadura durante la aplicación y ajustar los parámetros si es necesario.
g. Se debe monitorear la temperatura del metal base del componente para asegurar que se mantengan los rangos especificados en el procedimiento “WPS”.
h. Después de terminar la aplicación de metal duro, se debe permitir que el componente se enfríe lentamente en canastas aisladas o colchas de acuerdo procedimiento de enfriamiento especificado por el “WPS”. Este aislante no debe removerse hasta que el componente alcance una temperatura de 300°F, verificado con el sensor de temperatura calibrado.
3.22.5 Requerimientos de Pos-Soldadura
3.22.5.1 Inspección de la Calidad de Soldado
El metal duro aplicado debe inspeccionarse visualmente, verificando lo siguiente:
a. Porosidad, Huecos, y Sopladuras: Cualquier hueco o agujero en el metal duro mayor de 1/16 pulgadas en diámetro es rechazable (ver figura 3.22.1). También es causa de rechazo si existe astillamiento o levantamiento del material soldado.
b. Perfil de la Banda Soldada: Se debe verificar el perfil de la banda soldada con una regla recta, y debe estar plana o ligeramente convexa y consistente a través de todo el metal duro. Los perfiles cóncavos son causa de rechazo. Las bandas de soldadura que tengan ́jorobas ̈ significantes en el centro pueden repararse por esmerilado si fuera práctico (ver figura 3.22.2).
c. Amarre (Tie-in): Las bandas de soldadura deben amarrarse al material base y a las otras bandas de manera consistente y sin huecos profundos. Los surcos o huecos en el lugar de pegado (banda de “hardbanding” al metal base y entre bandas de metal duro) debe ser menor de 1/8 pulgadas de ancho y 1/16 pulgadas de profundidad. Se pueden reparar áreas pequeñas de amarre inadecuado por soldadura de punto antes de que el componente se enfríe, pero la reparación de soldaduras no debe continuar más de 45° alrededor de la circunferencia del componente (ver figura 3.22.3).
d. Modos de Agrietamiento: Se debe examinar el modelo de agrietamiento en el metal duro terminado y comparado con el modelo de agrietamiento aceptable especificado por el procedimiento “WPS”. Cualquier modelo de agrietamiento rechazado por la especificación del fabricante o no mencionado por la especificación es causa de rechazo.
3.22.5.2 La geometría de la Soldadura
La geometría de la soldadura aplicada debe cumplir con las especificaciones del cliente. Típicamente, el metal duro puede ser ya sea al ras (flush) con el “OD” del componente o resaltado (proud) por 3/32 pulgadas (+ 1/32 pulg.), medido dos veces separadas por 90º. Cualquier metal duro en la pendiente de 18º de la caja debe estar al ras para evitar dañar los elevadores (ver figura 3.22.4). Otras características aceptables y no- aceptables para algunos productos típicos de metal duro se ilustran en las figuras 3.22.5 a la 3.22.15
3.22.5.3 Inspección con Luz Negra
El componente endurecido y la conexión más cercana al endurecimiento aplicado (si está presente) se deben inspeccionar utilizando el método de inspección de conexión con luz negra (procedimiento 3.15). Cualquier grieta o indicios similares a grietas en las áreas no endurecidas son motivo de rechazo.


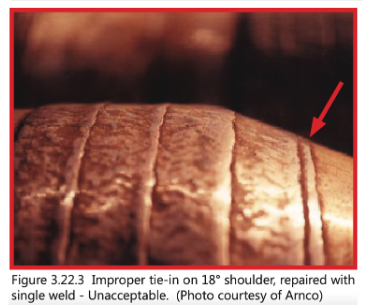
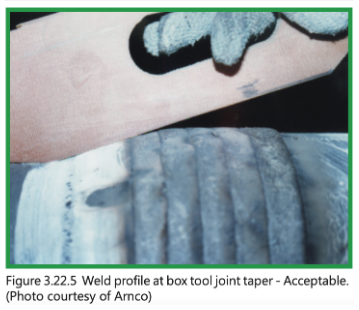



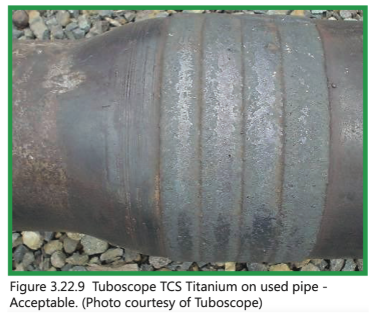
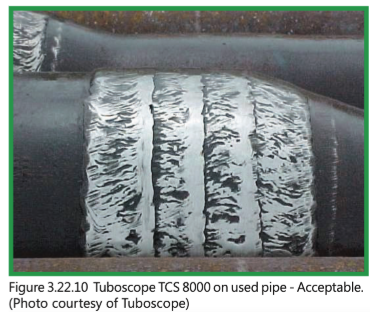

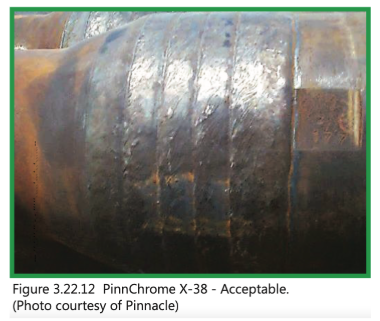



5.3 Desgaste de casing
El desgaste del casing es la remoción no deseada de metal del casing que resulta de la transferencia de energía de la sarta de perforación al casing durante la rotación y el viaje. (Aunque las operaciones con wireline también pueden causar desgaste de la tubería de revestimiento, el desgaste inducido por la tubería del cable no está cubierto en esta norma). El desgaste de la tubería de revestimiento es proporcional tanto a la fuerza normal entre el tool joint y la tubería de revestimiento como a la distancia relativa recorrida entre los dos. Por lo general, la distancia se desliza por el tool joint durante el viaje es pequeña en comparación con la distancia que el tool joint giratoria "slides" a través de la tubería de revestimiento durante la perforación
y “backreaming” el escariado. Por otro lado, la fuerza normal suele ser mayor durante el viaje, por lo que el diseñador debe preocuparse por el desgaste tanto durante la perforación como durante el viaje. El mismo mecanismo que causa el desgaste de la tubería de revestimiento también puede causar desgaste en los tool joints de la tubería de perforación, lo que puede reducir la resistencia a la torsión de la sarta de perforación. Los elementos esenciales detrás del desgaste de la carcasa incluyen:
• Fuerzas secundarias: Las cargas laterales entre la junta de la herramienta y la carcasa deben estar presentes si la carcasa se va a desgastar. El grado de desgaste será proporcional a la magnitud de la carga lateral, otras cosas iguales.
• Factor de desgaste: El factor de desgaste es otro elemento clave para determinar la tasa de desgaste de la carcasa. El factor de desgaste está muy influenciado tanto por el material de la junta de la herramienta como por las propiedades del fluido de perforación. La necesidad de reducir el factor de desgaste ha impulsado el uso de bandas duras "amigables" en las juntas de las herramientas.
• Cantidad de movimiento relativo: El grado de desgaste de la carcasa es proporcional a la distancia total a la que la sarta de perforación se desliza en contacto con la carcasa.
5.3.1 Volumen y profundidad de desgaste
El volumen de desgaste está dado por la Ecuación 5.1.

Una vez que el volumen de desgaste se establece mediante la ecuación 5.1, es necesario convertirlo en una reducción del grosor de la pared. Para hacer esto, primero calcule el área de la sección transversal eliminada usando la ecuación 5.2

Para calcular la profundidad de desgaste, se asume un patrón de desgaste como el que se muestra en la Figura 5.2, y el área de desgaste dada por la Ecuación 5.2 se establece igual a la siguiente relación:

5.3.2 Investigación sobre el desgaste actual de la carcasa
El modelo de desgaste de la carcasa presentado anteriormente (Ecuación 5.1) se basa en el trabajo realizado por Maurer Engineering bajo Proyecto DEA 42. ¿Trabajo más reciente de Hall & Malloy'? Indica que este modelo pierde precisión cuando se considera el desgaste de la carcasa a lo largo del tiempo, al menos en pruebas de laboratorio. Se ha propuesto un modelo diferente que introduce el concepto de un umbral de presión de contacto. De acuerdo con el modelo de umbral de presión de contacto, el desgaste es impulsado por la presión de contacto en lugar de la fuerza de contacto (o carga lateral) como en el modelo Maurer. La presión de contacto se define por el ancho de la ranura de desgaste (dos veces la dimensión "*" que se muestra en la Figura 5.2) y la carga lateral aplicada:
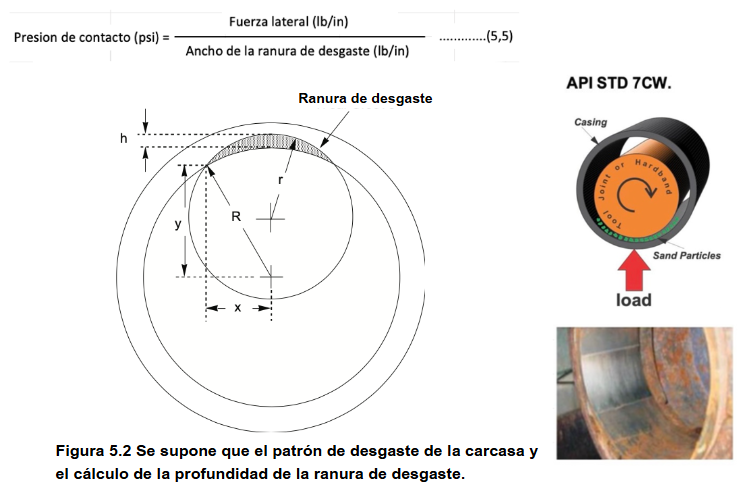
Es teóricamente infinito. A medida que la junta de la herramienta desgasta la carcasa, se desarrolla una ranura de desgaste con un cierto ancho y profundidad. A medida que el ancho de la ranura de desgaste crece, la presión de contacto disminuirá (suponiendo que la carga lateral se mantenga constante). Por lo tanto, es posible que la junta de la herramienta desgaste una ranura a un cierto ancho y profundidad que reduzca la presión de contacto por debajo del umbral, y no se produzca ningún desgaste adicional más allá de ese punto (de nuevo, dada una carga lateral constante).
5.3.3 Pruebas de desgaste de la carcasa actual
Además de los cambios en el modelo de desgaste de la carcasa, las pruebas reales han sufrido algunos cambios desde el Proyecto 42 original de la DEA. En general, los procedimientos de prueba más nuevos que se han desarrollado hacen varias mejoras incrementales que hacen que los resultados de las pruebas sean más confiables y repetibles. Desafortunadamente, eso significa que los datos de prueba más antiguos y los datos de prueba más nuevos tienen un conjunto diferente de parámetros básicos de prueba, lo que afecta a los resultados de la prueba.
Solo los resultados de la prueba adquiridos bajo el mismo procedimiento de prueba (es decir, nuevo con nuevo, viejo con viejo) se pueden utilizar de forma inteligente para evaluar múltiples opciones de bandas duras.
Más recientemente (en 2015), API ha publicado un estándar 7CW que proporciona un método para el desgaste de la carcasa de laboratorio y las pruebas de desgaste de las articulaciones de las herramientas. Esto ayuda a estandarizar un procedimiento reproducible para que lo use toda la industria, pero crea otro conjunto de parámetros de prueba que es diferente tanto de los resultados originales del Proyecto 42 de la DEA como de otras pruebas realizadas en el ínterin. Cualquier resultado de la prueba presentado debe considerarse cuidadosamente a la luz del tipo real de prueba realizada.
5.3.4 Términos de desgaste de la carcasa
Debido a las metodologías y teorías cambiantes, los términos utilizados para describir la eficacia de un determinado producto en la prevención del desgaste de la carcasa pueden ser ambiguos y confusos.
A continuación se muestra una lista de términos típicos utilizados para describir los resultados de las pruebas de laboratorio que se definen y explican.
5.3.4.1 Factor de desgaste
Como se discutió anteriormente, los resultados originales del Proyecto 42 de la DEA llevaron a un modelo de desgaste de la carcasa que relacionaba las cantidades medibles (la carga lateral y la distancia se deslizaron hasta el desgaste de la carcasa a través de un número determinado empíricamente que se llamó el "factor de desgaste". Debido a los desarrollos recientes, ahora hay múltiples factores de desgaste que se pueden informar:
a. Factor de desgaste de la carcasa / Factor de desgaste Hall: Este es el factor de desgaste de la carcasa original definido por el Proyecto 42 de la DEA. Es una relación entre el volumen de acero desgastado de la carcasa y el trabajo de fricción realizado
por la junta de herramienta en la carcasa, durante el 8 Prueba de desgaste de la carcasa de una hora. Tiene unidades de 1/psi y se describe mediante una reordenación de la Ecuación 5.1:

b. Factor de desgaste de la carcasa modificado / Factor de desgaste de la carcasa de Mohr: Esta modificación del número de factor de desgaste original intenta tener en cuenta los cambios en el rendimiento de desgaste debido a la dureza del material más suave (normalmente la carcasa). Por lo tanto, el factor de desgaste de la carcasa se multiplica por la dureza de Brinell (convertida en unidades de psi), produciendo un número adimensional.

Cualquiera de estos números de factor de desgaste de la carcasa se puede utilizar para comparar el rendimiento de desgaste de diferentes productos de bandas duras. Sin embargo, se debe utilizar la misma definición del factor de desgaste de la carcasa para la comparación; no compare un factor de desgaste de la carcasa/Hall con un factor de desgaste de la carcasa modificado/Mor. Además, las metodologías de prueba deben ser las mismas para ambos casos de prueba (antiguos en comparación con viejos, nuevos a nuevos). Los factores de desgaste más altos indican más desgaste o un peor rendimiento.
5.3.4.2 Porcentaje de desgaste de la carcasa normalizada
Las muestras de prueba de carcasa y bandas duras se pueden hacer en muchos tamaños diferentes, lo que cambia la cantidad de desgaste que se encuentra durante la prueba de laboratorio. La "normalización" es el proceso de convertir matemáticamente los resultados reales de la prueba a lo que los resultados de la prueba habrían sido en una geometría de prueba estándar (típicamente una junta de herramienta de 6-1/4” en una carcasa de 9-5/8” , 53,5#).
5.3.4.3 Ancho/profundidad máxima (estado estacionario) de la ranura de desgaste
Utilizando los datos recopilados durante la prueba estándar de 8 horas, la curva de profundidad de la ranura de desgaste frente a la curva de tiempo se ajusta utilizando la siguiente relación exponencial:

Donde:
h= Profundidad de la ranura de desgaste en función del tiempo
t= Tiempo
DU= La profundidad máxima de la ranura de desgaste en estado estacionario o máximo
EU= Un coeficiente de tiempo empírico
FU= Un coeficiente de tiempo empírico
Por lo tanto, se determina la profundidad máxima de la ranura de desgaste (DU), o "profundidad de la ranura de desgaste en estado estacionario". Físicamente, esta es la profundidad de la ranura de desgaste en el punto en el que el aumento del tamaño de la ranura de desgaste hace que la presión de contacto caiga por debajo del umbral para que no se produzca más desgaste. Esto no suele ocurrir en el período de prueba estándar de 8 horas, sino que se extrapola a partir de los datos de la prueba.
La profundidad de la ranura de desgaste en estado estacionario está relacionada con el ancho de la ranura de desgaste en estado estacionario por la geometría de la muestra de prueba, por lo que el ancho se puede calcular fácilmente a partir de la profundidad:
5.3.4.4 Revoluciones estimadas hasta 87,5 % de RBW de la carcasa / 12,5 % de desgaste de la carcasa
Si el ancho calculado es mayor que el ancho de la junta de la herramienta, entonces eso indica que no hay un límite físico para la cantidad de desgaste que experimentará la carcasa. En otras palabras, nunca se alcanzará el umbral de presión de contacto, y eventualmente se desgastará un agujero en el lado de la carcasa (dados los parámetros de prueba actuales).
5.3.4.5 Energía específica
El modelo original de desgaste de la carcasa utilizado por el Proyecto 42 de la DEA se puede expresar de una manera ligeramente diferente: se aplica energía de fricción a la carcasa, lo que hace que el material de la carcasa se desgaste. La relación entre estos dos valores (trabajo profesional/energía y volumen de material de la carcasa eliminado) es el factor de desgaste de la carcasa. Matemáticamente, esto es idéntico al modelo de desgaste dado en 5.3.4 porque el trabajo de fricción es igual a la fuerza de fricción veces la distancia deslizada. Por lo tanto, las dos formas de escribir el factor de desgaste de la carcasa de Hall son:

Por lo tanto, la energía específica de una determinada situación de prueba se puede utilizar como un parámetro de rendimiento de desgaste, por lo que las energías específicas más altas indican un mejor rendimiento.
5.3.5 Comparación del factor de desgaste/umbral de presión de contacto
Naturalmente, surge la pregunta de si los dos tipos de indicadores de rendimiento de bandas duras, el factor de desgaste de la carcasa más antiguo y el nuevo umbral de presión de contacto, se correlacionan entre sí. Es decir, ¿un producto de bandas duras con un buen factor de desgaste también tiene un buen umbral de presión de contacto?
Aunque no hay una ecuación analítica que se pueda utilizar para convertir el factor de desgaste en un umbral de presión de contacto, por lo general, las bandas duras con un factor de desgaste bajo tienden a mostrar un umbral de presión de contacto alto.
5.4 Control del desgaste de la carcasa
Para controlar el desgaste de la carcasa, el diseñador debe minimizar los tres elementos de la Ecuación 5.1 que rigen el volumen de metal eliminado: fuerzas laterales, factor de desgaste y distancia de la junta de la herramienta y la guía de la carcasa entre sí. La evaluación de estos factores y la preparación para controlar el desgaste de la carcasa deben hacerse en la etapa de planificación del pozo.
5.4.1 Minimizar las fuerzas secundarias
Varias acciones pueden reducir las cargas laterales entre la junta de la herramienta y la carcasa.
a. Optimizar la trayectoria: El programa de torque y arrastre utilizado para el diseño de la sarta de perforación tendrá una salida que mostrará la carga lateral en función de la profundidad. Examine esta salida para ver dónde están las cargas laterales más altas. Si el programa también tiene un módulo que calcula el desgaste de la carcasa, úselo para estimar la gravedad potencial del problema. Tenga en cuenta que cualquier estimación que utilice para el factor de desgaste probablemente será cruda.
La trayectoria de la trayectoria planificada a menudo se puede modificar para reducir las cargas laterales, aunque cambiar la trayectoria para lograr este fin puede tener efectos negativos en otras Cuestiones importantes. Por ejemplo, una mayor tensión axial en la sarta de perforación a través de una curva dará como resultado más fuerza lateral en la mayoría de los casos. Por lo tanto, cuanto más bajo en el agujero se pueda colocar una pata de perro planificada, menor será la carga lateral que causará y menos tiempo se dedicará a perforar a través de ella, otras cosas son iguales. Sin embargo, un punto de inicio más bajo requerirá una tasa de construcción más alta o una sección de construcción más larga para alcanzar un objetivo determinado. También dará como resultado una trayectoria de pozo más larga y un ángulo tangente más alto. Si en el equilibrio el diseño se mejora con un dogleg inferior dependerá de las circunstancias de cada caso. En resumen, la optimización de la trayectoria es un proceso complejo que intenta equilibrar muchas necesidades en conflicto, con la importancia relativa de todas las necesidades que varía significativamente de un caso a otro. "El esfuerzo también requiere un programa informático que sea capaz de integrar la mayoría de los problemas conflictivos en un solo cálculo. Cómo optimizar una trayectoria está fuera del alcance de esta norma, pero su impacto en el desgaste de la carcasa es muy importante.
b. Reducir la tortuosidad: las ondulaciones en el camino del pozo se llaman tortuosidad. Es muy útil si el programa de torque y arrastre permite variar la tortuosidad para ver su efecto en las cargas laterales. Si este efecto es significativo, el diseñador puede planificar varias acciones para minimizar la tortuosidad. Las causas comunes del problema son las correcciones de dirección, el dardo de la broca y la formación de salientes en estratos blandos y duros entre capas. El diseñador puede considerar conjuntos de dirección giratoria para facilitar las correcciones de dirección. El dardo de broca es el movimiento de la broca de un lado del agujero al otro que puede ocurrir si el BHA permite el movimiento lateral y El medidor de brocas y el medidor de agujeros no coinciden. Un conjunto de orificio lleno reducirá o eliminará el dardo de la broca, y puede disminuir la tendencia a formar repisas.
c. Ejecute los dispositivos de distribución de carga como los protectores de tubos de perforación: Además de redistribuir la carga lejos de las juntas de las herramientas, estos dispositivos también pueden ofrecer factores de desgaste más bajos, como se muestra en la Figura 5.3.
d. Evite el pandeo de la carcasa: se supone que la sarta de la carcasa se diseñará y aterrizará para que se mantenga estable.
5.4.2 Minimizando el factor de desgaste
El factor de desgaste es el segundo componente clave en los cálculos de desgaste de la carcasa. Hasta el conocimiento del escritor, no hay fórmulas para estimar el factor de desgaste en determinadas circunstancias.
Se determina experimentalmente en pruebas de laboratorio como las de la referencia 1. El aparato de prueba típico gira la muestra en un baño de lodo mientras se aplica una carga lateral medida.
Los datos de desgaste se registran y el factor de desgaste se calcula de nuevo utilizando la Ecuación 5.1. Una investigación considerable, en particular por parte de Maurer Engineering como el Proyecto 4212 de la DEA, ha explorado la relación entre las propiedades físicas de los materiales en contacto y la tasa de desgaste. En estos estudios, se demostró que la tasa de desgaste de las juntas de herramientas de acero desnudas era sorprendentemente alta, y mientras que el carburo de tungsteno grueso protegía las juntas de las herramientas de bandas duras del desgaste, dañó rápidamente la carcasa.
Se demostró que los materiales de bandas duras patentados "amigables con la carcasa" reducen el desgaste de la carcasa y la junta de la herramienta simultáneamente. Las figuras 5.3 y 5.4 muestran algunos datos publicados en la referencia 1. Como se muestra en la Figura 5.4, la tasa de desgaste también se ve muy afectada por las propiedades del fluido de perforación.
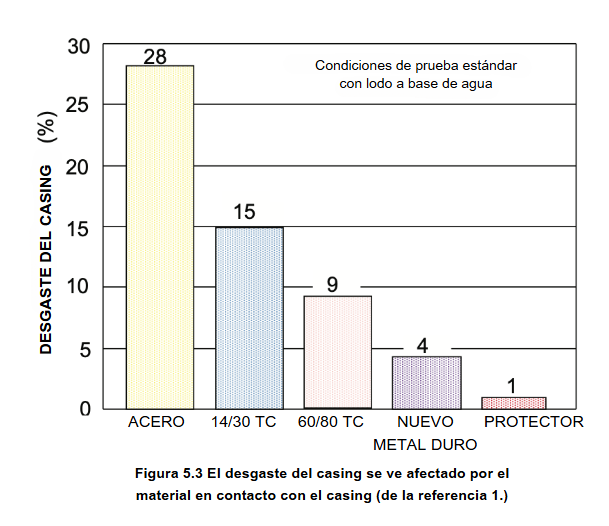

La referencia 1 muestra un rendimiento de desgaste considerablemente mejor para el lodo a base de aceite en comparación con el agua, aunque en otros estudios. * se llegó a la conclusión opuesta. La diferencia tal vez radica en las diferentes condiciones de prueba, lo que debería advertir al diseñador sobre la aplicación de factores de desgaste directamente desde el laboratorio en el campo. Schoenmakers Concluyó que los factores de desgaste determinados por el laboratorio se pueden aplicar a las situaciones de campo para predecir el desgaste real de la carcasa si las condiciones de la prueba coinciden estrechamente con las del campo. A menos que El diseñador sabe que este es el caso, sin embargo, los resultados de la prueba son probablemente más útiles para determinar la mejora o el deterioro esperado en el desgaste de un conjunto de circunstancias a otro. En resumen, alguna combinación de las siguientes acciones puede ayudar a minimizar el factor de desgaste.
a. Ejecute un material de bandas duras "amigable con la cubierta" en las juntas de las herramientas.
b. Utilice protectores de tubos de perforación.
c. Modifique el sistema de lodo para obtener una mejor lubricación.
5.5.1 Factor de desgaste/Características de desgaste
La prueba del factor de desgaste de la carcasa descrita en el párrafo 5.4.2 también prueba la resistencia al desgaste de la junta de herramienta. El fabricante del producto de endurecimiento debería poder proporcionar datos de prueba y cálculos del factor de desgaste (y otras características) de su producto. Cabe señalar que, a menos que las condiciones del laboratorio sean muy cercanas a las condiciones del fondo del pozo, estos números generalmente solo son útiles para comparar. Los factores de prueba a considerar incluyen el acabado de la superficie previa a la prueba y las dimensiones de las muestras de banda dura, las propiedades y dimensiones del material de la carcasa. , las cargas de fuerza lateral que se aplican entre la muestra de prueba y el material de la carcasa, la velocidad de rotación (rpm) de la muestra de prueba (y/o la muestra de la carcasa), las propiedades del fluido de prueba y el contenido de sólidos, el período de asentamiento de la muestra, y la duración de la prueba.
5.5.2 Tipo de banda dura
Los datos del factor de desgaste que se dan en la sección de desgaste de la carcasa muestran varios tipos de bandas duras, en particular el carburo de tungsteno (en diferentes tamaños) y un "nuevo metal duro" que fue uno de los primeros productos de bandas duras "amigables de la carcasa". Para describir con más detalle las opciones disponibles para un diseñador, a continuación se dan varios tipos comunes de bandas duras. Tenga en cuenta que estos no representan todas las opciones metalúrgicas, sino simplemente una instantánea de las categorías actuales de la industria.
a. Bandas duras a base de carburo de tungsteno: El carburo de tungsteno es un material muy duro que se dispersa en una matriz de metal de soldadura más suave en la junta de la herramienta para proporcionar resistencia al desgaste. Carburo de tungsteno El bandado duro se utiliza típicamente en formaciones muy duras o abrasivas en el agujero abierto, donde el desgaste de la carcasa no es una preocupación. La banda dura de carburo de tungsteno se clasifica según las propias partículas de carburo de tungsteno utilizando dos descripciones: forma y tamaño de la pantalla (o malla). La forma de la partícula puede ser sinterada, que está rota y angular, o esférica. Las partículas esféricas proporcionan esencialmente la misma protección contra el desgaste para la junta de la herramienta mientras se usa la carcasa a una velocidad más lenta, por lo que siempre se prefieren a la forma sinterizada. La pantalla de partículas o el tamaño de la malla define el rango de tamaño real de las partículas, generalmente en cuatro rangos: Grueso (20-30), medio grueso (30-40), medio (40-60) y fino (60-80). Por lo general, se prefieren las tallas más finas porque tienden a desgastar el casing a un ritmo mas lento.
Tenga en cuenta que, incluso en el mejor de los casos (partículas esféricas finas), las bandas duras de carburo de tungsteno siguen siendo extremadamente abrasivas y peligrosas en términos de desgaste de la carcasa. En general, se debe evitar su uso.
5.4.3 Movimiento relativo entre el revestimiento y la sarta de perforación
El desgaste de la carcasa también es directamente proporcional al movimiento relativo total entre las dos superficies de contacto. Cualquier cosa que reduzca el movimiento relativo entre la carcasa y la sarta de perforación reducirá proporcionalmente el desgaste de la carcasa. Los pasos beneficiosos incluirían aumentar la tasa de penetración y reducir las RPM, aunque estos pasos pueden ser mutuamente excluyentes. Para determinar la distancia total que se deslizó durante la perforación rotativa, primero calcule el tiempo que una junta de la herramienta está en contacto con un punto particular de la carcasa utilizando la ecuación 5.11. Utilice la Ecuación 5.12 para convertir el tiempo de contacto a la distancia deslizada durante la perforación rotativa.

5.4.4 Peso y calidad de la carcasa
Un revestimiento más grueso no reduce el desgaste del revestimiento, pero agregar espesor de pared puede permitir una mayor tolerancia al desgaste y dar como resultado una mayor capacidad de presión del revestimiento durante y después de la perforación. Contrariamente a lo esperado, White y Dawson4 encontraron una relación inversa entre la tasa de desgaste y el grado de la carcasa. Es decir, las carcasas de mayor calidad tendían a desgastarse más rápidamente. Por lo tanto, el diseñador no debe suponer que una carcasa de mayor calidad tendrá un mejor comportamiento frente al desgaste o una mayor capacidad de carga después del desgaste.
10.59.5 Procedimiento de inspección
Cada área con bandas duras se inspeccionará visualmente para detectar imperfecciones en toda la superficie con bandas duras. Esta inspección se puede realizar como una inspección separada o en conjunto con otras inspecciones visuales requeridas del elemento de la columna de perforación.
Inspeccione para detectar imperfecciones visualmente detectables. Las imperfecciones incluyen, entre otras, grietas, porosidad, orificios de soplado, cráteres, virutas de carburo elevadas, piezas faltantes o rotas, forma inadecuada del cordón de soldadura y profundidad inadecuada del valle entre pasadas.
Cuando se detecten visualmente grietas o secciones faltantes, se deberán examinar para asegurarse de que el material adyacente a la grieta no esté comenzando a separarse del material base.
Todas las grietas detectadas se examinarán para verificar que terminen dentro del cordón de soldadura y no se extiendan al material base en ninguno de los extremos del depósito de endurecimiento.
La porosidad se considerará excesiva cuando se vean tres o más orificios mayores de 3,2 mm (0,125 pulg.) dentro de un área de 12,7 mm (0,500 pulg.) de diámetro y la distancia entre los orificios sea menor que el diámetro de los orificios. Una porosidad excesiva puede dar como resultado una pérdida de resistencia al desgaste de la banda dura y puede causar erosión y/o lavado de fluido dentro de la propia banda dura. Esta condición deberá ser notificada al propietario/usuario.
Además de lo anterior para un endurecimiento “amigable con la carcasa”, el endurecimiento aplicado al área del cono del elevador de 18° de las juntas de herramientas en caja en la tubería de perforación y HWDP se debe examinar para verificar que haya un hombro claramente discernible con el diámetro exterior de la junta de herramientas alrededor de toda la circunferencia. Esta área también se revisa para ver si la banda dura está nivelada con la superficie adyacente del cono y si hay evidencia de un ángulo de hombro incorrecto. Una regla colocada a lo largo del hombro ayuda a detectar el nivel y el ángulo.
10.59.6 Procedimientos de evaluación y clasificación
10.59.6.1 Generalidades
Cualquier tubería de perforación, HWDP, collares de perforación o componentes de BHA que tengan bandas duras rechazadas según los criterios especificados a continuación se marcarán y se apartarán para disposición del propietario/usuario.
10.59.6.2 Criterios aplicables a todas las bandas duras
Todas las grietas que se pueda demostrar que se han propagado al material original serán motivo de rechazo.
Se rechazará cualquier banda dura que parezca no estar adherida o adherida adecuadamente a la superficie a la que se aplicó. Esta condición puede manifestarse por indicaciones visuales del depósito de soldadura de bandas duras que muestra signos de levantamiento de la superficie a la que se aplicó.
El diámetro exterior de las bandas duras se examinará visualmente para determinar cuánto queda. Si la banda dura está desgastada en cualquier lugar a lo largo de su longitud, se debe verificar el diámetro de la herramienta en ese lugar para asegurarse de que esté dentro de las tolerancias permitidas. Si el diámetro está dentro de las tolerancias aceptables, la condición de las bandas duras se anotará como "desgastada" en el informe de inspección, pero a menos que el propietario/usuario especifique lo contrario, esto no será motivo de rechazo.
10.59.6.3 Criterios para el endurecimiento con bandas duras de carburo de tungsteno
Es aceptable el agrietamiento confinado al metal endurecido. Las virutas de carburo que sobresalgan de la superficie del hard-banding serán motivo de rechazo.
El propietario/usuario podrá aplicar criterios de aceptación/rechazo adicionales, que pueden incluir, entre otros:
la zona de cobertura a la que se aplica la banda dura;
las dimensiones y tolerancias del grado en que las bandas rígidas deberán quedar al mismo nivel o elevadas por encima de las superficies adyacentes;
la anchura del depósito de soldadura y la profundidad y anchura de los valles entre pasadas de soldadura;
la concavidad del cordón de soldadura;
el alcance de las imperfecciones superficiales permitidas, como poros, perforaciones y cráteres;
el tamaño y la forma de las partículas de carburo de tungsteno utilizadas;
cualquier fisura aceptable o inaceptable en la superficie del endurecimiento acabado.
10.59.6.4 Criterios para la inspección de superficies con bandas duras “aptas para el revestimiento”
10.59.6.4.1 Generalidades
Cualquier tubería de perforación, HWDP, collares de perforación o componentes de BHA que tengan bandas duras rechazadas según los criterios especificados en 10.59.6.4.2 a 10.59.6.4.6 se marcarán y se apartarán para disposición del propietario/usuario.10.59.6.4.2 Ancho de grieta
Los criterios de rechazo son los siguientes:
si el ancho de cualquier grieta longitudinal u oblicua es superior a 1,0 mm (0,040 pulg.);
si el ancho de cualquier grieta transversal o circunferencial es mayor que 0,025 mm (0,010 pulg.).
10.59.6.4.3 Porosidad (orificios)
Se rechazarán los poros que tengan más de 1,6 mm (0,062 pulgadas) de diámetro y más de 1,6 mm (0,062 pulgadas) de profundidad.
10.59.6.4.4 Superposición y planitud del cordón
Los cordones deben superponerse ligeramente para evitar valles excesivos entre cordones adyacentes. Los valles entre cordones adyacentes no deben tener más de 1,59 mm (0,062 pulgadas) de ancho, medidos desde los bordes superiores de los valles, ni más de 3,17 mm (0,125 pulgadas) de profundidad. La forma de la cuenta debe ser de plana a ligeramente convexa. La concavidad en el centro de un cordón no debe exceder los 0,4 mm (0,015 pulg.).
10.59.6.4.5 Criterios de usuario/propietario
Los inspectores contratados para inspeccionar las bandas duras “amigables con la carcasa” deben consultar con el usuario/propietario para conocer criterios adicionales basados en las bandas duras específicas utilizadas y la experiencia de campo con esas bandas duras.
Los criterios adicionales pueden incluir criterios que limiten la longitud y el número de grietas. Ejemplos de criterios adicionales incluyen, entre otros, los siguientes:
donde hay más de tres grietas longitudinales que son tan largas como el ancho de un cordón de soldadura, independientemente del ancho de la grieta, que se concentran dentro de una longitud de banda circunferencia continua de 25 mm (1,0 pulg.) alrededor de la circunferencia del objeto donde se aplica la banda dura;
donde dos grietas longitudinales que son tan largas como el ancho de un cordón de soldadura están más juntas que 6 mm (0,250 pulgadas) en cualquier punto, y una o ambas tienen más de 0,5 mm (0,020 pulgadas) de ancho;
si alguna grieta longitudinal continua tiene una longitud superior a 50 mm (2,0 pulg.);
cuando las grietas orientadas transversalmente se cruzan con más de una grieta longitudinal u oblicua;
donde las grietas orientadas oblicuamente se cruzan con una grieta longitudinal y una transversal.


10.59.6.4.6 Bandas duras aplicadas al área del cono del elevador de 18° de las juntas de herramientas en caja en la tubería de perforación y el HWDP
Los criterios de aceptación y rechazo para la superficie con bandas duras del área del cono del elevador de 18° en juntas de herramientas en caja en tubería de perforación y HWDP serán los siguientes.
a) La transición entre el cono del elevador de 18° y el diámetro exterior de la junta de herramienta debe tener una esquina discernible alrededor de toda la circunferencia donde se cruzan el diámetro exterior de la junta de herramienta y el cono del elevador.
b) Si durante la inspección se revela evidencia de un ángulo incorrecto, el cono del elevador de 18° se medirá con un transportador biselado y estará dentro de una tolerancia de o se rechazará.
c) La superficie con banda dura en el cono elevador de 18° deberá estar al ras con la superficie adyacente del se estrechará hasta una tolerancia de o se rechazará.
d) Se rechazará cualquier hard-banding que parezca no estar correctamente adherido o adherido a la superficie a la que se aplicó.
Autor:
Juan Manuel Ortiz Rosero
Ingeniero Industrial
Visítanos Hoy Mismo
Explora nuestra tienda online en www .itpprecision .com y descubre cómo podemos ayudarte a optimizar tus operaciones. Contáctanos para más información, y únete a nuestra misión de combinar eficiencia y obtener sostenibilidad en cada paso del camino.
Síguenos en nuestras redes sociales para mantenerte al día con lo último en innovación industrial:
Facebook: @ITPPrecision
Instagram: @ITPPrecision
Tik Tok: @ITPPrecision
Youtube: @ITPPrecision
Pinterest: @ITPPrecision
Linkedin: @ITPPrecision
Telegram: @ITPPrecision
Whatsapp: @ITPPrecision
Al seguirnos, estarás al tanto de nuevas soluciones, promociones exclusivas y artículos técnicos que te ayudarán a optimizar tus procesos industriales.
🔹 #NDT
Commenti